Warehouses – the Achilles’ heel in net zero?
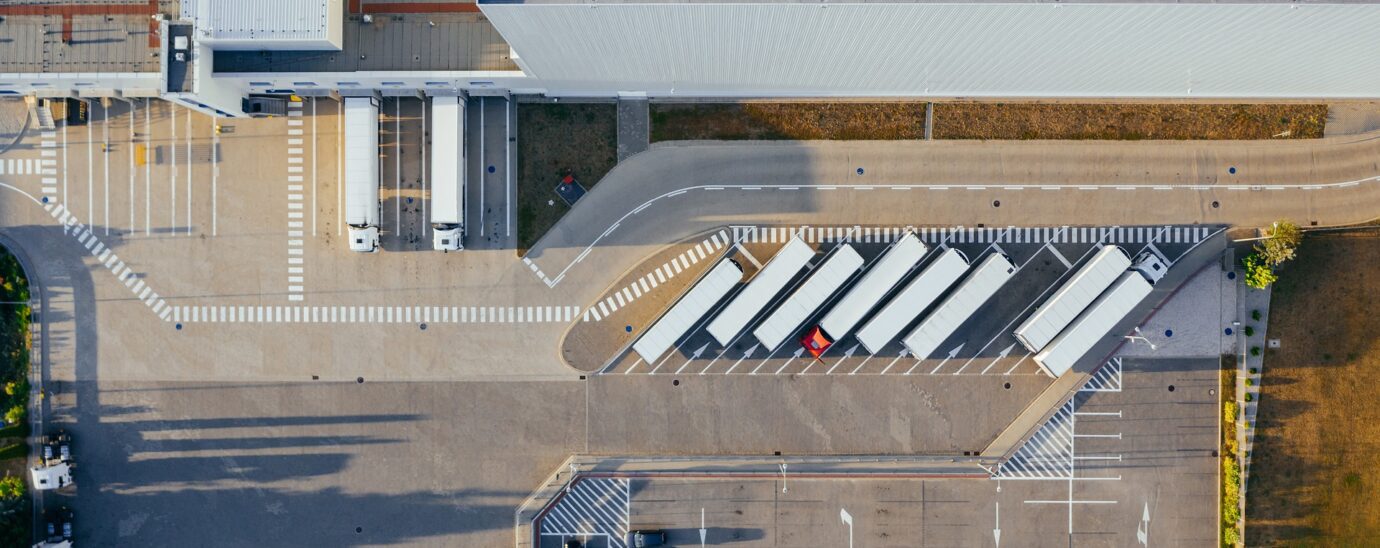
Over the past few years, retailers have taken huge strides to understand and address the environmental impact of the supply chain. In a bid to achieve Net Zero objectives, a shift to domestic and near-shore production is reducing carbon emissions and a focus on reducing empty miles in both inbound and last-mile deliveries is improving green performance.
Yet in the middle of this process is the warehouse. From heat and lighting to packaging and miles. moved around the site, warehouses can often represent a black hole when it comes to sustainability measures. With rising costs and an escalating labor shortage on top of green expectations, retailers can no longer overlook warehouse inefficiency of any kind.
From cobots to slotting optimization and task interleaving, Alex MacPherson, Director of Solution Consulting and Account Management at Manhattan Associates, outlines the significant opportunities to improve both efficiency and environmental performance that will support brands looking at their overall, end-to-end environmental impact.
End-to-End Challenge
Business’ environmental awareness and commitments are increasing fast. In response to customer expectations, growing shareholder demands for greener business models and punitive regulations, Net Zero pledges are now a core component of the corporate strategy.
For retailers, however, every aspect of the business model is inherently environmentally unfriendly.
Products are often shipped from China or Asia, transported around increasingly complex supply chains that encompass distribution centers, local hub warehouses, and stores, as well as the challenging last mile of delivery to the customer door. Furthermore, the explosion in eCommerce has added even more complexity and cost – both financial and environmental.
Over the last 18 months, retailers have worked hard to achieve significant improvements to both their inbound and outbound transportation processes: companies have reduced their reliance on Eastern manufacturing to achieve more agility and reduce travel miles too; consolidators are encouraging retailers to work together to maximize shipment fill and minimize empty miles; and customers are being encouraged to embrace ‘slower’ delivery models, with intelligent route scheduling enabling retailers to offer lower-cost greener deliveries while nudging behavioral change in a more sustainable direction.
Environmental Sump
The warehouse, however, remains a significant challenge to any Net Zero goals. These enormous buildings have doors open at each end – inbound and outbound – day and night, adding a massive heating overhead to the 24×7 lighting demands. With the rise in eCommerce, packaging usage has skyrocketed – a shocking one-third of all solid waste in the US is eCommerce packaging.
Steps have been taken to mitigate some environmental impact with a number of green housekeeping adopted in the majority of large warehouse sites. LED lighting is standard, insulation has been improved. Rainwater harvesting is becoming more commonplace, alongside solar panels and wind turbines too.
The majority of packaging material that arrives within warehouses is now recycled; although, many retailers are still wrestling with the challenges of creating outbound packaging that is both recyclable and robust enough to be undamaged in transit. Further improvements in the technology of recyclable materials will no doubt continue apace and offer retailers wider choices in the future.
It is within the warehouse that significant process review and overhaul could now make a significant contribution to reducing the carbon footprint and moving closer to Net-Zero.
Automation Imperative
Growing numbers of retailers are looking to accelerate automation plans – although in many cases these are spurred by the challenges created by labor shortages and rising costs rather than environmental goals. Certainly, the eradication of paper-based picking should be a priority for any site yet to make that move – alongside the removal of paper packing slips. With the right underpinning technology – including emailed receipts and online returns options – the process is more efficient, lower cost, and greener.
Automation can also transform the efficient use of forklift trucks that transport goods miles around the warehouse. While trucks are, in the main, battery-powered, inefficient technology combined with poor charging routines places huge demands for electricity on these sites, making it imperative to optimize every journey.
A Warehouse Management System (WMS) that includes task interleaving can minimize forklift empty journeys by routing the driver to both drop-off and pick-up pallets in one journey. In addition to radically improving efficiency and cutting the carbon footprint, the WMS can also match tasks to labor management to optimize battery charging within a shift and maximize the efficiency of each truck.
Intelligent Planning
Slotting optimization can also transform the efficiency of the overall warehouse design. By comparing product turnover, including seasonal and promotional demand, with the warehouse layout, the WMS can optimize slot location to minimize the walk length – by foot and truck – improving efficiency and reducing costs, as well as cutting the carbon footprint. Intelligent evaluation of replenishment models can also be a revelation. Is it more efficient to opt for fewer full pallets, rather than multiple half pallet replenishments for certain stock items, for example?
Embedding returns management into the WMS, with touchscreen scanning and validation, can also transform the speed with which returned goods are repatriated to the supply chain – cutting costs and, critically, minimizing the amount of stock that is sent to landfill.
Taking this broader view of efficiency, including a reduced carbon footprint as well as productivity and cost, is also providing key insight for companies exploring robotics to further expand automation. The biggest growth in this area is cobots, typically operating as pickers and transferring the goods to human packers. In addition to reduced errors and improved efficiency, the ability to hire cobots on demand, or ‘robots as a service, is helping companies to manage labor shortages.
Conclusion
While there is certainly a great deal of innovation in the industry, it is nevertheless vital to address much of the in-built inefficiency across the retail supply chain.
Minimizing the number of half-full shipping containers – traveling in both directions – is a priority for the industry, as is improving customer education and awareness regarding greener delivery.
As on-time delivery becomes more important than speed, it will be interesting to see whether retailers start to default to green delivery, compelling customers to request more environmentally friendly options.
It is within the warehouse, however, that the biggest changes are required and potentially the biggest gains to be made. While solar panels and recycled packaging are a good starting point, they are not an end destination. Retailers now have the opportunity to take a radical approach to warehouse automation as well, in the process of moving ever closer to meeting targets for Net-Zero.
ENDS