LPAs Key To Manufacturing Recovery
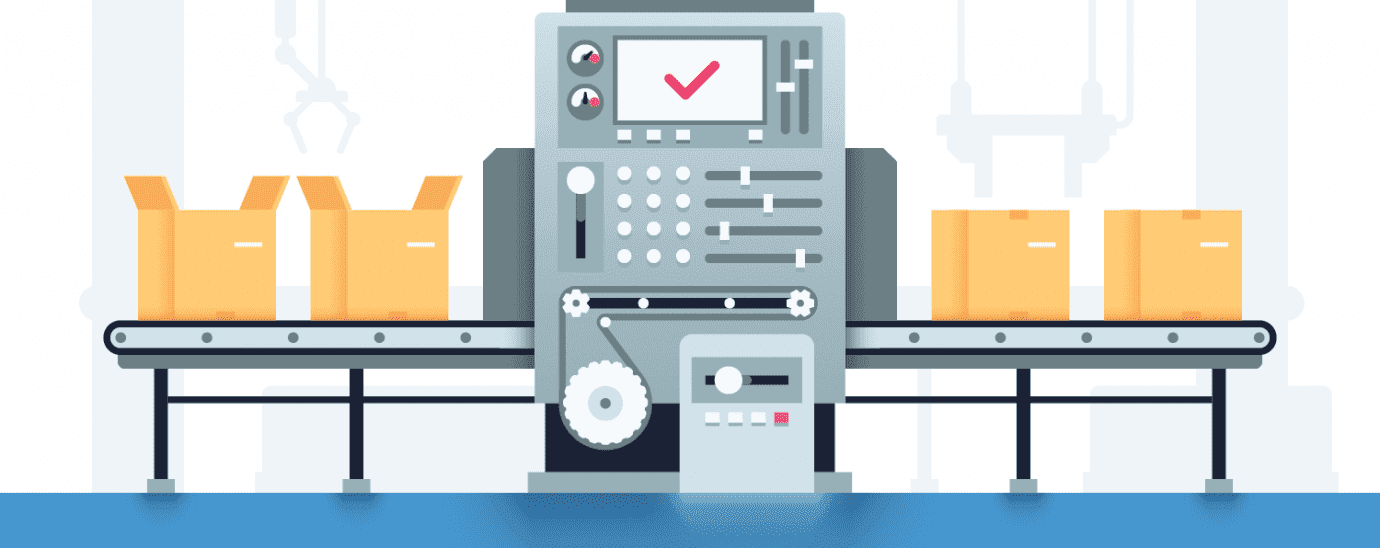
LPAs hold the key to greater product quality and a faster manufacturing recovery
As UK manufacturing continues its recovery from the pandemic’s impact, its factory production growth is simultaneously being slowed by Brexit-hit supply chain disruption. Between Brexit and COVID, movement between borders is slowed. This has culminated in the manufacturing industry recording its slowest output rate for nine months, in February. It’s clear that factories need to boost efficiency and productivity, and increasing quality is one way to do this.
And the need for greater quality is no longer optional. The UK Government has announced that a new Right to Repair law will come into effect this summer. In a bid to increase the life span of electrical products, companies will legally have to make spare parts available to consumers for the first time. This places further pressures on supply chains and demands for quality on an already hindered manufacturing sector.
Digitally transforming the UK’s factories
To meet quality targets and increase efficiency with fewer resources, factories must embrace digital transformation .
Research suggests 74% of manufacturers accept that they need to adopt digital technologies in order to prosper. but with the manufacturing industry hit hard by the current economic climate, the pace of change needs to be stepped up.
One effective measure is the wider introduction of Layered Process Audits (LPAs). Used by the automotive industry for many years and now finding their way into other manufacturing sectors, LPAs are a vital tool for increasing productivity and ensuring quality is maintained consistently.
What exactly is an LPA?
An LPA is a quality technique that focuses on observing and validating how products are made rather than inspecting finished products. LPAs are not confined to the Quality Department. Rather, they involve all employees in the auditing process. Supervisors conduct frequent process audits in their own area, while higher-level managers conduct the same audits less frequently and over a broader range of areas.
LPAs help manufacturers and service providers take control of processes, reduce mistakes, and improve both work quality and the bottom line. But are they being utilised effectively by businesses? And is there enough awareness around exactly how LPAs can benefit manufacturers by helping them standardise processes?
Currently, I would argue there isn’t. But to aid recovery and increase efficiency, there needs to be.
The benefits of LPAs
If you bake a cake, you follow the instructions on the side of the box. You set the oven to the temperature it says, you know what ingredients to mix because you want a controlled output. If you throw the ingredients together without the right recipe and process, however, you’ll be disappointed with the outcome. It’s the same philosophy in manufacturing.
Organisations with robust LPA programs in place see significantly lower rework and scrap, fewer warranty holdbacks, and reduced customer complaints.
The underlying causes of most manufacturing issues are a lack of process standardisation or a failure to follow these approved processes. The key to improvement is to define these standards and create systems that ensure those processes are followed correctly.
By conducting multiple layers of the same audit, an LPA system helps ensure that the audits are conducted accurately because the auditors are essentially double-checking each other. And by including multiple layers of management, the company demonstrates that quality is important to everyone.
Creating effective LPAs
If we think back to the baking analogy again, to create an effective LPA system you must be constantly looking for opportunities to enhance the recipe and make it even better.
One of the fundamental make or break components of an effective LPA is the questions that auditors ask. A good LPA should have between 10 and 15 yes or no questions focused on processes critical to quality, performance, or customer satisfaction.
Many companies, particularly those using old paper-based checklists, rely on overly generic questions that yield limited insights. They do this so they can use the same checklist for multiple work areas, when a best practices approach is to create separate checklists for each area. But even a well-written LPA is nothing if it’s not embraced by the workplace.
It’s important with any manufacturing process, but especially with LPAs, that you foster a culture where good quality is rewarded and championed, rather than bad quality punished. Everyone needs to be on board to succeed, taking pride in carrying out LPAs and actively making suggestions on how they can be improved.
By digitalising LPAs with layered process audit software and making them a key part of a factory’s digital transformation, data can be delivered to plant floor decision-makers in real-time, LPAs can become quicker and cheaper to carry out, and risk identified earlier. It can also help to give greater management visibility and ultimately engage employees. It is crucial the manufacturing sector strives for zero-defects – in other words, ensure products are made correctly first time, every time. This will save the industry countless hours and massive amounts of money in reproducing defective products. LPAs are an extremely effective tool in driving towards zero defects.
Identifying weaknesses and overcoming challenges
In a recent Ease webinar looking at reducing reoccurring defects with an LPA check-up, we asked the audience to vote on the biggest barriers they are facing to effective LPAs in their organisations. Interestingly, the findings show us that aside from poor questions and tracking capabilities at the setup and implementation phase, the biggest roadblocks are around culture and lack of support from senior management. To me, these aren’t issues with LPAs themselves, but systemic issues faced across the manufacturing industry surrounding all processes and performance.
Digital transformation, driven by LPAs, has the power to drive a swifter and stronger recovery for our manufacturing industry, but it starts with people. If we can create collaborative, positive factory environments, where people of all levels strive for quality, underpinned by strong process and technology, the UK’s manufacturing industry can shake off the COVID and Brexit shackles, fire up its engines and emerge better and stronger for it. It’s time to act now, before any more damage is done.
- TPIs are the Future of Energy Solutions
- Quick Commerce and the Retail Media Revolution
- How Construction Companies Can Leverage Cloud Bursting
- Is It Time for a VMware Alternative?
- AI Leads as VivaTech Unveils Top 100 Startups